Rinsing Bottles and Cans
We offer bottle and can rinsers, where glass and PET bottles are rinsed in a rotary unit and the cans with the use of a gravity rinser.
Bottle-Rinsing
Rottary Rinsing Machine with 48 nozzles
​
​The unit is a rotary rinsing machine and it has 48 rinsing nozzles to wash inside the non-returnable glass bottles ranging from 250 cc up to 1000 cc.
The operating speed of the machine is from 8,000 up to 20,000 bottles per hour.
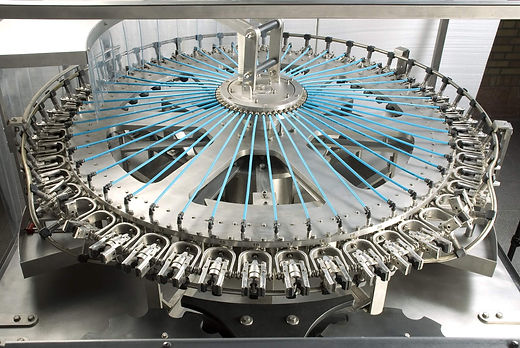


-
Fully automatic operation by PLC control.
-
Colour touch screen panel.
-
Electronic speed change in main drive motor with frequency inverter.
-
Error diagnostic system.
-
Inside of bottles are washed by spraying water in a single-phase rinsing process.
-
All the surfaces in contact with “water” made of AISI 304 stainless steel.
-
Polyamide gears to reduce noise and vibration.
-
Easy changeover of spare parts.
-
Safety guards made of AISI 304 stainless steel with tempered glass.
Can-Rinsing
W-Twist Gravity Can Rinser with water or air (ionized)
​
The Rinser stands for reliability in plants with a production speed of up to 120.000 cans per hour. The great advantage is the simple adjustability of the rinser for beverage cans or food cans in all common dimensions and materials.
Adjustment takes place pneumatically and mechanically via a hand crank at the infeed and discharge turner as well as in the rinser channel. Manual changing of e.g. spirals is no longer necessary.
Cleaning media is water, ionized air or cleaning fluids on request.



-
The containers are fed via various conveyor belts – air or chain transport.
-
The empty cans are turned 135 degrees at the rinser head in the inlet and fed into the rinser channel.
-
In the rinser channel, the empty cans are rinsed out with water or ionized air in the upper third.
-
In the lower two thirds, dripping takes place in the water rinser in order to achieve the specified value for the residual water content. For cleaning with ionized air a second blow unit can be added in this section.
-
After the cans have been cleaned, they are turned back again by the discharge rinser head (standing on the can bottom) and transferred to the conveyor belt.
-
The adjustment is quick, easy and reproducible and takes approx.1 to 2 minutes.